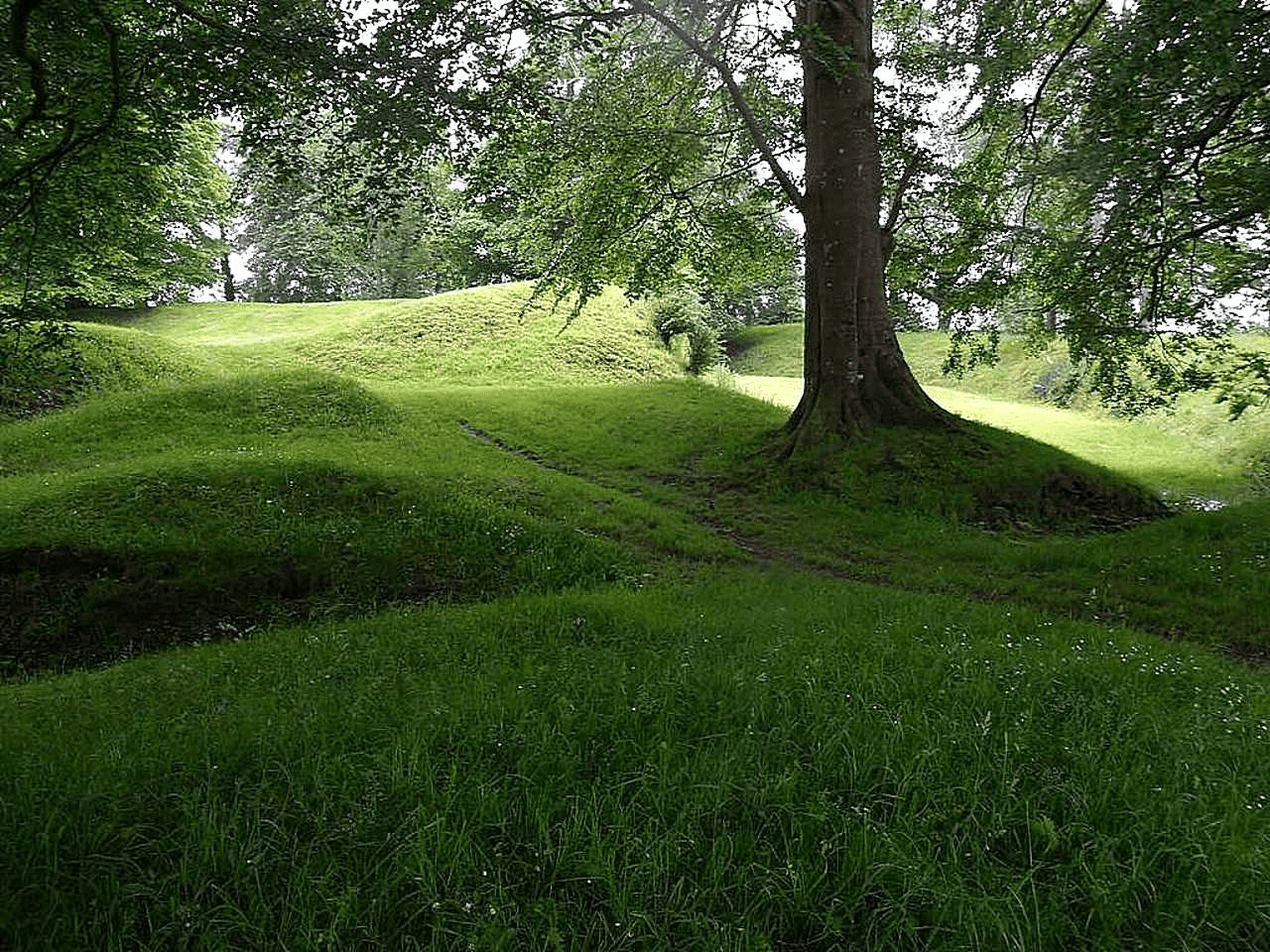
The Aero Squadron Lounge – wiring
Nothing brings a miniature build together quite like lights, but wiring a structure always has challenges.
This was my first time working with builders foam for landscaping and building walls, but it won’t be my last. It was a great material for hard wiring the lighting, too.
Before I glued the base of The Aero Squadron Lounge onto the landscaping board, I cut wire channels that would run underneath. I draped twine inside the channels so I could tie the wires to it and then pull the wires through the channels later in the build. You’ve probably noticed these strings in the posts I’ve been writing about the tower and main room construction.
The front door carriage lamp was the first light to be installed but I don’t have good photos of what I did.
I poked a bamboo skewer into the foam to make a wire channel and pulled the wire up toward the roof. I used the skewer to then make a channel toward the join with the tower. On the side of the front wall, I cut a channel into the foam so the wires would run toward the ground and through the baseboard channel.
Fortunately, I did take better pictures when I wired the three hanging lights over the three tables inside. For the one over the pub table by the front door, I cut a channel into the balsa wood beam and pulled the wire through the front wall. I then painted the wire to match the beam. This was the only wire that might possibly be noticeable if left white.
For the other two hanging lights, the roof rafters covered the channels made in their respective beams.
I cut a channel into the builders foam all along the top edge leading toward the earlier channel made for the front door carriage lamp.
I used a length of tubing to feed the wires through the channel.
I taped all the wires to the twine and pulled the twine through the channel.
Once I cut the twine from the wires, I fed them into the side baseboard channel toward the back and to the power strip. The remaining length of twine here is for the tower light.
I pressed the wires into the side wall channel on the front wall. Once the tower was attached, this would be sealed up with stucco.
The front spotlight was fairly straightforward as well. I bought a pack of two Scene Master spotlights on amazon.com but used only one of the pair included in the package.
Once I knew where I wanted the spotlight, I cut a further channel to it from the other baseboard channel. I ran a length of wire underneath the house and left a small bit exposed to wire the light. I had to plant the grass before I could install it.
I filled in the channel with leftover stucco when I added the dogwood tree base, where I used stucco to sculpt the hill. I filled in the other front baseboard channel with stucco after attaching the tower. You can see where I adjusted the channel at the front of the board.
Once the grass was planted, I was able to wire the spotlight. I cut the spotlight wires short and then spliced them to the exposed wire from the ground.
I made a small hole in the ground to sink the spliced wires into.
I glued the spotlight to the grass over the hole.
As noted in a previous post, the bar lights are operated by a 9V battery.
To keep the bar removable, I wired the two lamps to a 9V battery adapter with an on/off switch from Evan Designs. Ingenious, right? Ha! There are two main issues with this idea. First, the bar is definitely removable, but it is hard to get it back into place without the wires sticking out…very fiddly. More importantly, the battery doesn’t last long and the candlesticks are very dim. I tried wiring each lamp to its own battery but the difference in brightness was negligible and it doubled the fiddly nature of trying to get the bar in place with two battery assemblies fighting for freedom. What I should have done was made a plug in the floor.
The lit fire is an acrylic log piece with a red bulb. I drilled a hole for the bulb to fit through the bottom of the egg carton hearth, and its wire runs inside a channel through the baseboard foam along the back.
Since the fireplace is removable, I have a small recess where the wire and bulb can curl into when the fireplace is removed.
However, now I see Minimum World has a battery operated flickering fire light that would certainly make removing the fireplace less of a hassle. (Update: I installed the Minimum World battery light here.)
Close-up of the recess and fireplace wire.
The most challenging light to wire was the tower light.
Even if I hadn’t made the tower roof removable in the end, I wanted exposed rafters and holes in the roof. That meant you would be able to see the wire, even if I cut a channel into the balsa beam and painted it.
I opted to hide the wire in plain sight with conduit made from 3/32″ aluminum tubing from my local hobby shop. I eliminated the chain on this light and made it a ceiling fixture. The wire goes up through the beam, through the conduit and out the side of the tower. The end wire runs between the tower and side wall, eventually to be covered with stucco.
To disguise the end of the wire inside, I used a round wooden bead. I painted the conduit on the beam brown to match the wood. I painted the conduit along the wall and the wooden bead warm white to make it blend in with the wall color. I have seen conduit done like this in real life many times. I added a metal doorbell from Sussex Crafts to act as a vintage light switch. Now the illusion is complete. The whole process is detailed in the tower construction post, part 3.
Here is the faux switch for the tower light.
I started to fill in the side baseboard channel with stucco but realized the moisture from the stucco might mess with the spliced wires and I didn’t want to take any chances. Instead, I cut a sliver of builders foam to plug the channel. These channels don’t have to be pretty, they just need to work and be hidden in the end.
Categories: The Aero Squadron Lounge
September 20, 2012 | 0 commentsThe Aero Squadron Lounge – removable fireplace
Or, turning stryofoam into stone. For the initial structure, I used regular white stryofoam for the side walls since it was easy to cut and shape with sandpaper.
I added builders foam across the front only because I had the perfect sized scrap for the opening. The back and upper sides are foam core board and the upper front is balsa…a little bit of everything from the scrap box.
The back of the fireplace is made from egg carton bricks placed in a herringbone pattern. As I had done for the Heritage chimney, I used a printed grid to help keep the pattern consistent.
The fireplace is actually bricked all the way up inside as you can see in this work-in-progress shot. I changed to regular brick pattern from the upper edge of the stone fireplace through to the top of the chimney opening.
I had to do this in two sections, the back and sides first and then the top front, which wasn’t glued in place until after all the painting and grouting was complete. Below, you can see the brick on the back and sides in progress as well as the initial coat of spackling on the stone portion of the fireplace.
I painted the bricks with Camel by Americana using a stencil brush to stipple on the paint. I did the same thing with Desert Sand by Americana, leaving some of the Camel underlayer showing here and there. I sealed the bricks with Delta Ceramcoat satin varnish and then used spackling for grout. I followed that with washes of browns and black to reach this coloration.
I was very heavy handed with the spackling on the fireplace.
After sanding, it really did start to look like real stone.
I then layered on paint washes, rubbing the surface with my fingers to make sure there were no brush marks left. I used an X-Acto knife to draw lines on the stone. I wanted it to appear to be made from stone slabs. Going over the lines with an awl chipped the stone and made the seam lines more realistic.
The fine detail is something I didn’t expect but just love about it. It now even feels cool to the touch like real stone.
I bricked, painted and grouted the interior of the front top piece (no photo unfortunately) and glued it in place. I then cut builders foam pieces to make the back wall that the fireplace would have been attached to at some point, with some extra broken bits to fill in the space.
This was painted and covered with stucco to match the rest of the building.
On the inside of the back foam piece, I scored the surface to mimic the egg carton brick on the interior. It was then painted to match. Here it is still wet from the paint washes.
I made the top front and sides of the broken chimney from scraps of builders foam, finishing in the same manner. Here they are before painting.
I then covered the front and sides with stucco to make a complete unit.
The lit fire is an acrylic log piece with a red bulb. I drilled the hole for the bulb through the bottom and later made a channel in the floor for it to curl out of sight when the fireplace is removed. More about that later.
The fireplace screen is by Jeannetta Kendall and purchased from lacyhome4boys on eBay. Here’s the shiny new screen in place; it looks like I built the fireplace around it but that’s just coincidence. :D I bought this as a last minute addition.
I used black acrylic paint to age it and tone down the shine. Much better.
The medallion above the fireplace is a jewelry finding. Overall, the fireplace is not that easily seen in the final layout, but I love it and think it adds so much.
Categories: The Aero Squadron Lounge
September 19, 2012 | 0 commentsThe Aero Squadron Lounge – structure, part 2
Continued from structural details, part 1 for The Aero Squadron Lounge.
I used regular household stucco patch from Home Depot to cover the walls inside and out. I eventually painted the stucco surfaces Warm White by Americana. In the photos for this post, you’ll see a lot of back and forth with painted and unpainted stucco. I applied most of the stucco while the walls were flat and left the areas where the walls would join clear.
I cut out a recess in the foam above the front door to leave room for a cross beam. As I had done for the window, I painted the area around the door opening green, applied the stucco and painted it before gluing the foam outer wall to the wood inner wall.
The original kit wall leading to the greenhouse had a square opening, but I cut the foam padding with an arch. I filled in the gap between the two layers with stucco so you couldn’t see where the square points had been. I later broke apart this wall’s back edge (right side in this photo) but I wasn’t sure how much I would need to keep the building complete…so I left it intact during the first part of construction.
I’ve detailed the tower construction, including its stonework, in separate posts starting here.
The spiral stairs inside the tower were added after the floor was secured to the base board but before the tower was attached. I have a more extensive blog post on the stairs here; these required a good amount of math and planning. :D
The front door from the kit originally had a window. I opted to make a solid door from balsa, scored to look like it was made from planks. I added a Z support structure on the inside.
I painted the door Clover by Folk Art with a light sanding afterward. The working hinges are from Olde Mountain Miniatures.
The flooring is made from 5/8″ x 1″ egg carton tiles. The fireplace hearth is a solid piece of egg carton material as well. It is attached to the fireplace but not to the main floor.
I painted and sealed the tiles before grouting with spackling, then added multiple washes to add depth to the coloration. The recess in the back is where the fireplace sits; I later painted it to blend in.
The fireplace unit is situated in the open back. To make this a 360° build, I added rubble walls to the back wall that tied in with the back edges of the side walls and the back of the fireplace. I was able to do this only because I planned for part of the roof to be open. This and the bombed out condition of the back wall would allow access inside the structure even when the fireplace is in.
Here you can see what is permanent to the building when the fireplace is removed.
And with the fireplace in.
Here you can see the broken side back wall near the greenhouse. I used flat nose pliers to rip pieces away at random before painting and grouting. This wasn’t easy as the builders foam was rather resistant to tearing. You can also see that when I joined the greenhouse to the main room, I applied stucco over the seams and around the base of the walls.
Continued in part 3.
Categories: The Aero Squadron Lounge
September 18, 2012 | 0 commentsHeritage – grandma’s neglected lawn, part 1
While I do have more builders foam in larger sheets, I thought I’d use up the numerous leftover scraps. They were just languishing in a bag and this would clear up some workspace. :D
I started cutting a puzzle of pieces to make the uneven ground surrounding the house.
If you recall, I had glued the house foundation onto cut pieces of 3/8″ plywood to allow room between the brick foundation and the base board.
You can see the edges of the plywood below the foundation.
The builders foam is 1/2″ thick, but I planned to sculpt it anyway. I cut random amounts from the foam pieces, angling the slope down sharply around the outer edge of the base board. Yes, that’s Grahame and Woodrow playing ball on the bay window. :D
No wonder grandma never mows the lawn…she’d break her ankle! It doesn’t matter if the pieces aren’t a perfect fit. I can fill in those gaps with either scraps of foam or a bit of stucco patch.
After using up most of the scraps, I cut a new piece for the larger remaining area, tracing out the base for the stone steps.
I saved the circular scrap from the tower for building up the area that will hold The Tree. Actually planting The Tree is going to take some work since part of the roots will be exposed and part will terminate under the surface.
I have the trunk fairly close to the house so that the branches stay within barrier of the base board. The side is less of a problem than the front. I keep one side of my landscape boards no wider than 25″ so the houses will fit through the doorways in my real life house.
I’ve cut the area in front of the steps lower to make room for the pavers that will be placed in front, but I can see it’s not very even. I’ll have to adjust that a little. Having broken, weedy pavers is one thing, but we don’t want a death trap at the end of the stairs. Grandma isn’t foolish.
Continued in Part 2.
Categories: The Haunted Heritage
September 17, 2012 | 0 commentsHeritage – hallway vignette
The balcony railing is still a work in progress so this upstairs ‘room’ isn’t yet complete, but I have finished the vignette that will sit to the left of the bathroom door.
The table is a House of Miniatures Hepplewhite Side table with hand painted designs and added elements inspired by a real life sized antique table.
The books are some of the many I made while filling the parlor bookcase.
The vase and bird figurine were purchased awhile ago, but I’m no longer sure of the vendor. The red dahlias were made from a Bonnie Lavish kit.
I made the tiny red alarm clock from bits and bobs. The face is a printed image from The Graphics Fairy with a clear cabochon sticker to simulate glass. I had made a set of vintage table clocks for another miniaturist through my etsy shop, and I liked the red one so well I knew I would need one for the Heritage.
The artwork is a photograph from artisan Natasha Fadeeva. She makes the most amazing little animals. I just swoon over her mice!!! :D I contacted her about using the vintage mouse photos in the Heritage, and she graciously gave me her permission. I haven’t yet framed the other.
I love the red and round theme of this vignette. :D
Categories: The Haunted Heritage
September 16, 2012 | 0 comments
NOTE: All content on otterine.com is copyrighted and may not be reproduced in part or in whole. It takes a lot of time and effort to write and photograph for my blog. Please ask permission before reproducing any of my content. Please click for copyright notice and Pinterest use.