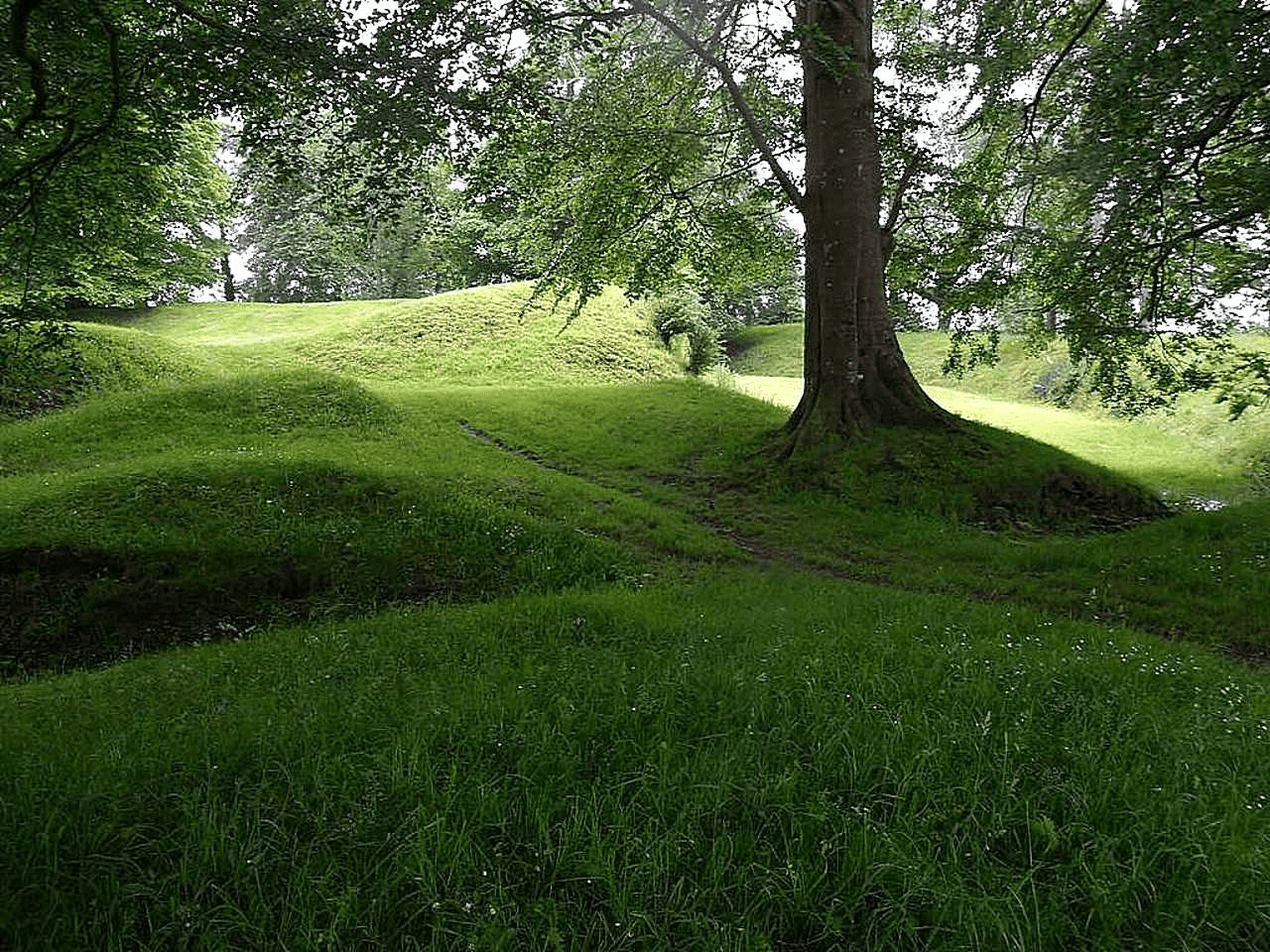
Mail Wagon – part 5
Continuing work on the Mail Wagon. I put together the rear axle assembly.
The front assembly required drilling a hole using the provided jig. I was able to use my hand tools – a pin vise – to make this hole. For the rear assembly, the metal was thicker and the pinvise was no match. I got a blister and two shallow pilot holes for my efforts. :\
To finish drilling the holes, I bought the Dremel chuck #4486, which holds bits with 1/32″ to 1/8″ shanks. The buggy kit provides a 1/32″ drill bit (shown here in the pin vise).
Since the metal parts are delicate and easily marred by pliers, I had to figure out a way to safely hold the assembly while also not breaking any of the parts already assembled. I folded a small hand towel to protect and brace the assembly. I attempted to drill, and the metal wagon spring heated up fast, so I added a tipped clamp to hold and protect my fingers from the heat.
The first hole worked great since I had been able to get further into the metal with the pin vise. The other hole wanted to wander, so I had to work more with the pin vise to get the pilot hole deeper and in the right line. The excess hole will not be visible after assembly.
I reapplied the epoxy to the wood piece that sits on top of the wagon spring. I added the brass rods right away to make sure everything lined up properly while the epoxy set.
I added the square nuts and trimmed the brass rod to complete the rear axle assembly. It’s not very level or straight, but that is a limitation of the cast metal spring. It’s somewhat pliable, so it doesn’t want to hold the proper shape. I think it will be barely noticeable once the parts are painted a uniform color and the wagon cabin is added.
There is a spring for the front axle assembly, but that will have to be added later since I’m not using the reach (the rod that connects the front and rear axle assemblies). I’ll be making my own reach once I have the wagon cabin built, so the front spring will have to wait for now. Next up will be working on the wheels, which seems like it will labor intensive. If all turns out, they should be beautiful.
Categories: Ivy Hollow RFD, Model Cars, Vehicles
June 9, 2019 | 0 commentsMail Wagon – part 4
Continuing
to swear atwork on the Mail Wagon. To make it easier to work on the next part, I took closeup photos of the large schematics and printed the sections I needed. This eliminated the need to keep walking into the kitchen to look at the blueprint sized papers. I could sit and work in one area.The laser etched brass pieces add fantastic detail, but they are tiny and challenging to work with.
They fit well once you wrangle them into submission. I do worry about the longevity, even with using super glue. I think that’s because of how delicate the parts seem.
The bolts are made from another type of laser cut material. Fiddly, but again the detailing is wonderful.
I clipped the excess brass as recommended, and they do now look like tiny bolts. :]
The front axle assembly is done.
Next up, the rear axle assembly and wheels.
Categories: Ivy Hollow RFD, Model Cars, Vehicles
June 8, 2019 | 0 commentsMail Wagon – part 3
Continuing work on the Mail Wagon. I’m starting with the Doctor’s Buggy by Model Trailways. What I like about the kit are the well made parts, the detailed instructions and good pictures. I’m not much of a fan of the huge blueprint sized diagrams, though. I suppose it is easier from a manufacturing standpoint, but there isn’t always a lot of room to spread these things out while working. I have to keep them in another room and walk over to view them since I don’t want to keep clearing my workspace as I move back and forth between steps. As nice as it is to have large diagrams, the huge sheets are cumbersome. As usual, though, I made a photocopy of the regular sized instructions and diagrams so I can mark them up as needed.
Another issue is the lack of numbering on the individual parts on the wood sheets as well as the detailed diagrams. The detailed diagrams call the parts by their functional name but don’t indicate a number, so you have to look for a part that resembles the drawing among the wood sheets. It’s doable but inefficient. If I didn’t have the model building experience I do, this might be a bigger issue.
As noted before, I plan to make the front and rear axle assemblies, including the wheels, and then build my wagon cabin to suit. The instructions start with the axle assemblies, so that’s where I begin. You make a jig to help with drilling an accurate bolt hole. It’s a great feature of the kit.
The laser cut front axle cap is longer than the metal front axle, so I had to trim it to match the photo. The instructions mention nothing about this trimming, so luckily I had studied the photo.
In addition, the laser cut front axle cap and the metal front axle have slightly different bends. While the metal is somewhat pliable, it wasn’t possible to get a bond without gaps. After painting, this should be no issue. Since clamping was not possible without a lot of shifting (I used my fingers to hold the parts until the epoxy set), I glued the middle portion first.
I used Devcon 5 Minute Epoxy from amazon (as an Amazon Associate, I earn from qualifying purchases). This stuff stinks to high heaven with the hardener smelling like rancid, rotten eggs, but it is as advertised.
Once the epoxy set on the middle portion, I was able to go back and glue the ends. I held the pieces until the epoxy set, then for the final curing time, I clamped the hell out of it. :D
The rear axle cap and rear axle fit much better, but I had to trim the ends of the wood part here as well.
I need to swear at the instructions some more to figure out the next steps. Back soon…
Categories: Ivy Hollow RFD, Model Cars, Vehicles
May 25, 2019 | 0 commentsIvy Hollow – screen door, part 2
Continuing work on the screen door. I’m likely going to jump around a lot as I get going on the post office structure, furnishings, mail wagon and horse.
I had already ordered the Aluminum Black when Sheila said it worked well for her. She was right about the fumes, so into the garage this went. Bleh. (As an Amazon Associate, I earn from qualifying purchases.)
I did test it on a scrap first and the color seemed great.
I applied to the larger piece, and it was splotchy. I added a couple of coats, and that caused some issues. I even saw a puff of smoke or vapor at one point. :\
In the end, it didn’t work because the chemical was caustic enough to weaken the delicate screen. I can see how this would work well for more substantial material, but this material was just too thin. I cut a new screen insert and decided to just go with the original finish. I considered pouring some of the chemical into a dish, dipping it and then removing it, but I worried the finish would be splotchy again. Plus, it might still weaken the metal with only a quick dip. I have a few ideas.
Of course, now I know how to make an old deteriorating screen. :D
Categories: Ivy Hollow RFD
May 17, 2019 | 0 commentsChrysnbon kitchen hutch to desk
In the large group of magazines gifted to me recently, there are numerous articles on how to make more from a kit than what is presented in the instructions. I’ve modified kits before, but some of these are truly remarkable and have opened my eyes to even greater possibilities. I bought this Chrysnbon kitchen hutch kit at a local mini show.
In the November 2000 issue of Dollhouse Miniatures magazine, there are instructions for converting this hutch into a desk (and a shelving unit if you want to use all of the pieces). I think the vintage style is perfect.
I sorted the parts and have a nice bunch left over for later projects. I don’t know that I’ll make the wall cabinet from the spare parts, but you never know.
The instructions indicate to use the base back piece, but it has some issues with injection marks and you are to remove the ribs with a knife. These would not be highly visible under the desk, but they would be unsightly enough to bother me.
I could turn the piece around, but then the back would be rather ragged. Granted, the back the desk isn’t visible when in the room, but why bother with these issues at all when there’s a large piece in the leftovers that has wood texture on both sides?
I cut the large piece to minimize the injection marks. Much better. :]
After gluing the top to the sides and back using Testors plastic cement, I went my own direction using the magazine instructions as a general guide. Since I didn’t care about making the top cabinet, I used the spare parts as needed. It simplified things for me. I built a box for the side drawer and door.
I cut the original skirt as meant in the bash, but I made a solid piece for the right side.
Instead of using the remaining small drawers, I cut a new one from the spare parts.
I sanded the back of the door smooth so it would sit more in line with the new drawer. The one on the left shows what it looked like before the sanding.
That left the holes and imperfections on the left inner panel.
I thought it would be more difficult to fill with putty and get a good result, so I cut a board to cover the entire lower portion. Once painted, it will be less obvious.
More to come….
Categories: Furniture
May 12, 2019 | 0 comments
NOTE: All content on otterine.com is copyrighted and may not be reproduced in part or in whole. It takes a lot of time and effort to write and photograph for my blog. Please ask permission before reproducing any of my content. Please click for copyright notice and Pinterest use.