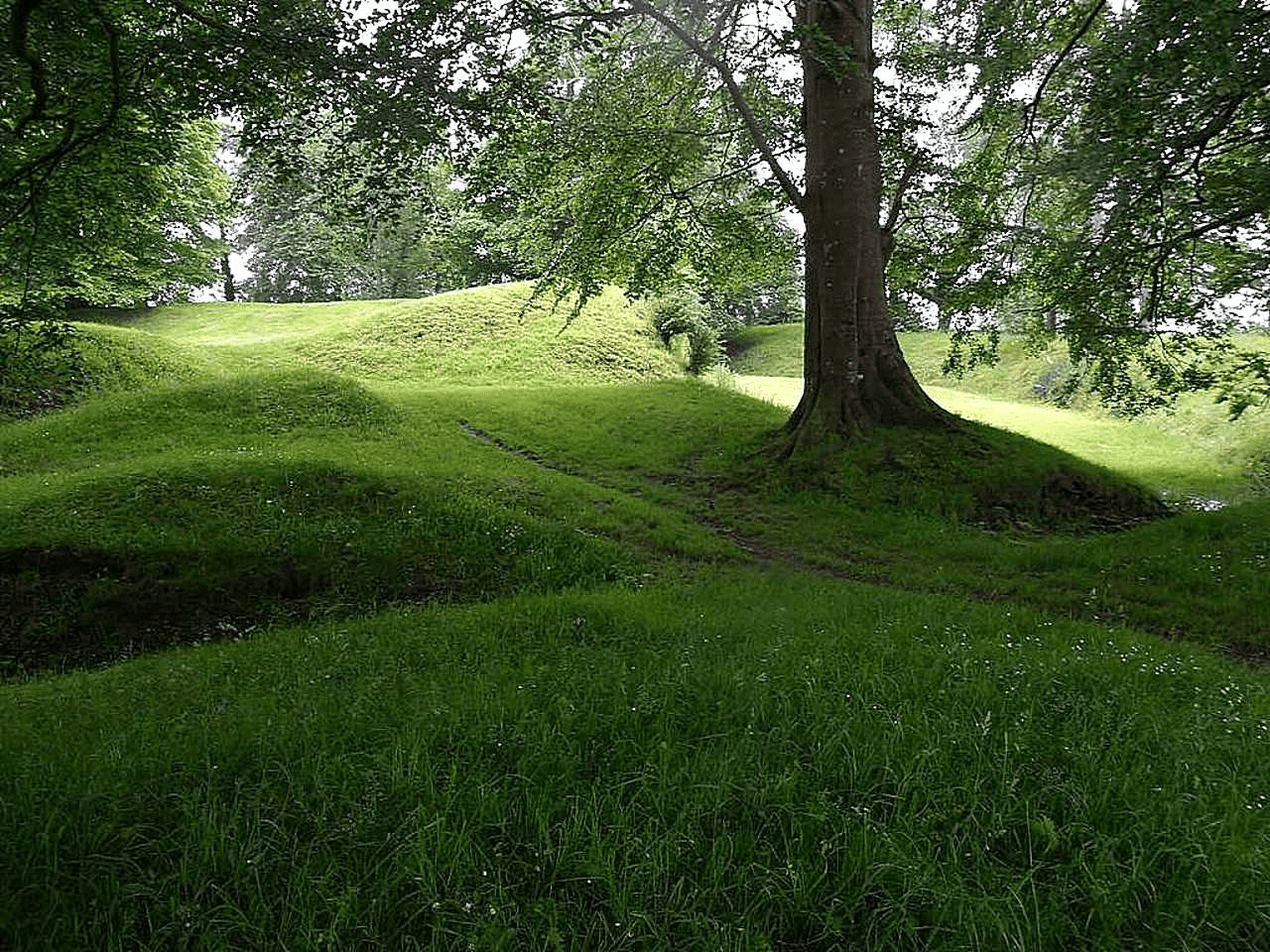
NOTE: All content on otterine.com is copyrighted and may not be reproduced in part or in whole. It takes a lot of time and effort to write and photograph for my blog. Please ask permission before reproducing any of my content. (More on copyright)
Categories:
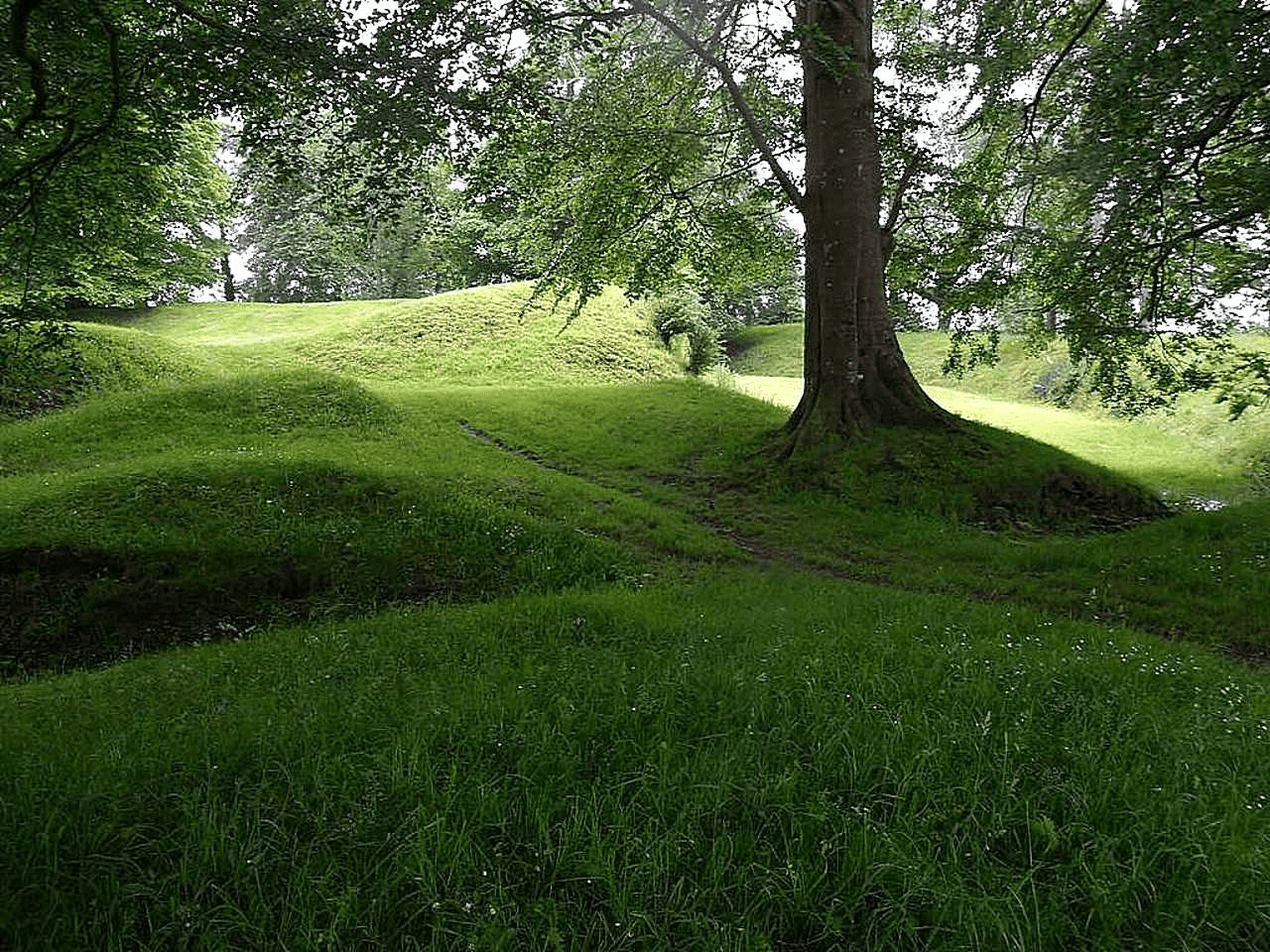
Ivy Hollow – screen door, part 4
Continuing work on the screen door. I was already leaning toward the micro mesh, but the overwhelming votes for it helped seal the deal! :D I tried a couple more tests to see if I could tone down the sheen. I tried to spray paint the mesh once before, but I figured I’d try some other types.
Left to right:
- Rust-Oleum Self-Etching Primer, which is a grey-green. It bonds to metal to serve as a base for better paint adhesion.
- Rust-Oleum Aluminum Primer, which is light grey. It bonds specifically to aluminum, which is the mesh material. I bought this to prime the wagon wheel hubs, which are aluminum.
- Model Master Metalizer Lacquer in Gunmetal, which is…errrmmm…gunmetal grey. :D It’s a buffing paint meant to give a true metallic finish, so the finish is also meant to rub off.
- Krylon Paint/Primer in flat black. The standard base coat.
And, here are the test samples. All very nice colors and no more sheen. Apparently, I was the problem when I tried painting this mesh before. haaaaaaaa. The paint adhered just fine without clogging the holes.
On the door, I think the clear choices for color are the Rust-Oleum Self-Etching Primer and Model Master Metalizer Lacquer in Gunmetal. Both remove the sheen and the results are not too light or too dark.
I think I will go with the Rust-Oleum Self-Etching Primer for the simple fact that it is made to bond to metal. The Model Master Metalizer Lacquer did rub off easily when I ran a paper towel across it, while the Rust-Oleum Self-Etching Primer stayed put.
Categories: Ivy Hollow RFD
July 30, 2019 | 0 commentsIvy Hollow – screen door, part 3
Continuing work on the screen door. When I left the screen door last, I had tried to darken the aluminum micro mesh without success. I moved on to the wood parts. I marked where the glue joins would be and left those unpainted as I gave the screen door boards a first coat of Woodland Green by Americana. It’s a satin paint, which means no need for a final varnish, but it goes on very thin and needs multiple coats. I painted the solid door the same color.
In the meantime, I continued my research and window shopping, happening across the best hay bales I had seen in miniature at Maple Leaf Miniatures. I wrote to the shop owner, and she got back to me with availability. Aren’t they marvelous? :D
While discussing my project, she offered some black screen material. Here it is next to the micro mesh. The scale is a bit larger, but the color is great. It also doesn’t get damaged just by looking at it the way the micro mesh does.
She also included some snacks for Jebediah! :D
Anyway, today I tested the two materials with the painted door.
It’s a hard choice. On the one hand, the black screen will be more durable and less obvious. But, the micro mesh is better for scale, and honestly, the damaged bits here and there rather add to the realism. There will be a cross bar in the middle and likely an angled brace, too. I think I will need to see how it looks with the door in dry fit with the building to make a final decision.
Categories: Ivy Hollow RFD
July 28, 2019 | 0 commentsIvy Hollow – potbelly stove, part 1
Many moons ago, I building a decrepit potbelly stove from a Chrysnbon kit for Baslow Ranch.
It’s a great kit, with a skinny stove that is perfect for a small structure. Typically, these would be placed in the middle of the building, but we’ve already planned the layout with the stove in the corner. This will have a newer look to it than the Baslow Ranch stove, but I still sanded the pieces with a fine grit sanding paper to remove the shine from the plastic.
I spray painted the pieces flat black, including the few factory silver parts included. I sprayed the scoop with Model Masters Aluminum Plate Metalizer. More on that in a later post. I assembled the bottom and top halves of the stove, then left them separate for now.
I want my stove to have coal light, but I have learned a lot since I made the Baslow Ranch stove. I used the red bulb included with the kit in that instance, but now I very rarely use anything with non-replaceable bulbs. LEDs and replaceable bulbs make for easier replacement if or when bulbs burn out. I wound three 1.8mm LEDs together – 3V flickering orange and yellow and a 7-19V separated steady red with a rectifier/resister. Since these are all 3V until they are connected to the rectifier/resistor, I am testing the lights with a 3V battery switch. [Note: If I were to do this again, I would make the third flickering bulb orange instead of yellow since the yellow was too bright in the end.]
I shortened the wires, combined the red and black bundles and spliced a new, single end wire to the bunch.
I wound the wires to form a base and taped it together with electrical tape.
I pulled the single end wire through the bottom of the stove and situated the lights inside. The assembly is not fixed in place just yet.
The light through the damper looks nice already, especially with the orange and yellow flickering over the steady red glow.
I will work on simulated coals next to diffuse the light a bit more, because you can see the bulbs from certain angles.
Categories: Ivy Hollow RFD
July 28, 2019 | 0 commentsMail Wagon – part 6
Continuing work on the Mail Wagon. With the front and rear axle assemblies started, it was time to work on the wheels. Most instructions tell you to read through the whole process before starting. This is to familiarize yourself with the parts and process. In this case, the instructions indicate it was noticed during the prototype stage, the manufacturer found it was easier to sand the spokes after assembly. That saves a lot of initial prep work on individual fiddly parts.
The wheels are made from laser cut wood parts, aluminum hubs and a jig.
I used MiniGraphics Wallpaper Mucilage to apply the paper patterns to the wood base. Here is the smaller wheel pattern. The larger wheel pattern is on the reverse, but in reality, you would work on one wheel at a time so it’s not an issue.
Another nice thing is the intact inner circle and middle “wheel” waste pieces. I saved those in my stash. Never know when I might need pieces like these. :]
I decided to use the recommended nails to hold the wheels in place while assembling. The paper pattern did not match up with the wheel size, so I centered as best as I could. Using the nails also helped keep the circular shape while working whereas clamps might not have.
Even though I will be doing the final shaping after assembly, I did clean the laser char from the edges of the spokes beforehand.
I did the same for the wheels to have a cleaner gluing surface.
That’s when things went off the rails. The spokes fit well into the hub, but overall the wheels, hubs and spokes simply did not work together. (These will have a snug fit, but I was just testing parts at this point and didn’t trim the spoke ends to fit all the way into the hub groove.)
The wheels are larger than the jig pattern as noted, and the spokes are too short. I am putting the parts together as instructed and have removed the parts precisely from the laser cut sheets without removing any length from the spokes.
I could use the “scrap” wheels between the two true wheels with the longer spokes, but that would give me only two wheels instead of four.
Luckily, this kit is made by a company still in business, so I sent them these photos and told them about my issues. They checked their production, and what they have now is correct. Mine must have been an errant batch. They sent me a new wheel sheet, another spoke sheet and four hubs just to make sure it all worked well together. It’s fantastic when a company will stand behind its product. :]
Now, I need to prep the new parts for assembly. Back soon….
Categories: Ivy Hollow RFD, Model Cars, Vehicles
July 17, 2019 | 0 commentsIvy Hollow – siding and gable bump out
Here’s a refresher on the postcard from 1917 showing a post office with RFD horse wagons picking up the mail. I want to keep most of the details of the original with a few changes.
I bought some half-scale Alessio Miniatures windows for the gables from Manchester Dollhouse and Wood Works. They are square instead of rectangular, but they fit my smaller, shorter structure well.
They fit perfectly with the 1/4″ thick walls, but I will need to adjust the depth with the siding in place.
The acrylic insert lifts out for easier finishing.
When HBS had their April Fool’s sale, I bought a pack of siding. It was way more than I needed for this building, but it’s a material I know I will use in the future and it was a great deal at 40% off.
I like to apply siding while the walls can be pressed flat for the best results, but if you do that, you have to take the corner joins into account. I’ve left excess on the overlapping edges – not to cover completely but enough to aid in construction later. The corners will be covered with trim. I use Elmer’s wood glue supplemented with dots of super glue gel to apply siding, taping the joins and edges, then pressing flat under magazines and books for at least 24 hours. Makes for a nice, flat wall.
For the window openings, I usually just cover the whole wall. I’ve tried piecing before, and it doesn’t end up saving you much in the long run for all the hassle. To get a cleaner cut, I hold the board up to the light to trace the outline.
I then make a scored cut along those marks with a fresh blade.
I finish cutting the window opening out from the back side.
This keeps the siding from splintering. The window trims cover any minor blemishes.
As you recall, I’ve flipped the building construction to better fit the horse. In the original, there’s a bump out in the gable over the angled door. I made a base for this from scrap wood. I’ll determine the final depth I need, add a surface board and then apply siding. I left enough space to apply siding to the part adjacent to the gable window.
Categories: Ivy Hollow RFD
July 10, 2019 | 0 comments
NOTE: All content on otterine.com is copyrighted and may not be reproduced in part or in whole. It takes a lot of time and effort to write and photograph for my blog. Please ask permission before reproducing any of my content. (More on copyright)